BASF Care Chemicals, who manages complex volume planning for nearly 3,000 products across a global network, implemented the Board Enterprise Planning Platform to streamline processes. This data-driven solution automates core calculations, identifies production bottlenecks, and facilitates integrated planning across departments. The platform has resulted in increased transparency, faster processes, improved decision-making, and a more reliable foundation for financial planning.
Using Board for volume planning facilitates the opportunity for accelerated realignment of product mix, by product to market, highlighting the opportunity for more profitable plans.
Anja Scheu
BASF, Project LeadBASF Care Chemicals division stands as one of the world’s largest chemical suppliers, specializing in premium ingredients and formulations for cosmetics, detergents, and cleaner industries. With a commitment to sustainable innovation, it also offers solutions for industrial formulators being applied in various industries like construction, and crop protection, addressing both current needs and future sustainability goals.
Navigating complexity in volume planning.
Volume planning at BASF Care Chemicals presents a formidable challenge. With over 3,000 products across 30 production sites, planners face a high degree of complexity. This intricate process, involving multi-stage production and global supply chains, significantly impacts downstream processes, including financial planning. Capacity bottlenecks loom at each stage of production, often disrupting existing plans and compounded by the uncertainties of the modern global supply chain. Consequently, the limitations of Excel-based global planning processes became increasingly apparent in managing this complexity. Recognizing the need for a transformative solution, the pioneers in sustainable solutions embarked on a comprehensive project, with the Board Enterprise Planning Platform playing a pivotal role.
Streamlining capacity-based volume planning.
To address these challenges, the company utilizes capacity-based volume planning, starting with independent demand planning. Regional account managers and marketing teams forecast market demand for the coming years, leveraging historical sales data, contribution margins, and current sales and revenue plans.
Capacity calculations then follow as volumes, agreed upon during demand planning, are allocated to available production facilities. Empowered by the new platform, the team determines raw material requirements and navigates multi-stage complexities. Notably, the platform detects and resolves issues such as circular references in bill of material (BOM) resolution for intermediate products.
Additionally, the team factors in varying production rates across the different plants, converting production hours into weight to determine achievable quantities. Optimal capacity utilization is then calculated, with potential bottlenecks identified and addressed through predefined calculations and workflows facilitated by the platform.
Selected production sites confirm agreed production quantities, seamlessly integrating them into subsequent planning processes to close off the loop.
However, theory alone cannot encapsulate the myriad factors influencing planning. Prioritizing intermediate products, considering economic aspects like contribution margins and past sales trends, and navigating supplier constraints and internal inventory limitations necessitate ongoing manual adjustments. These adjustments, transparently documented in the planning cycle, go through iterative refinement until volume planning is optimized, seamlessly feeding into operational financial planning and enhancing margin contribution and profitability.
The outcome is an integrated global financial planning framework underpinned by production facility allocation. Integral fields such as mid-year allocation, operational product planning, forecasting, portfolio simulation, and strategy development are all encompassed within this framework.
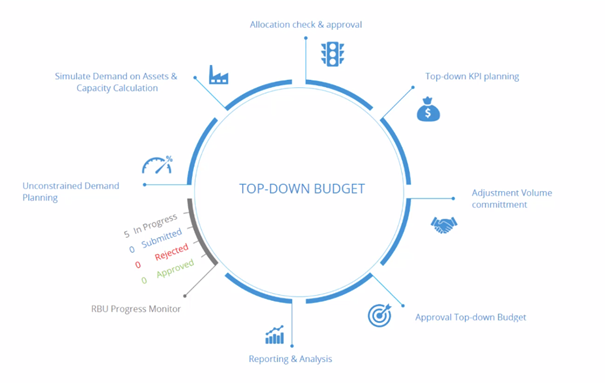
Comprehensive transparency through linked data.
The new platform consolidates data from previously disparate systems, unlocking enhanced transparency and accelerated processes across the different areas of the business. Product management gains agility in responding to demand fluctuations, seamlessly integrating changes into production capacity calculations and automating required intermediate products for an expedited planning process.
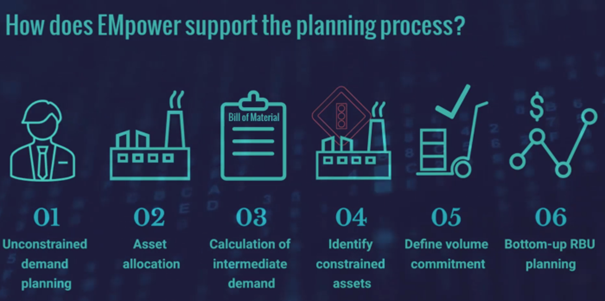
Portfolio management benefits from more visibility into the data, algorithms, and rules governing calculations, facilitating informed decision-making regarding product launches and production changes.
The platform also provides a reliable foundation for long-term planning, enabling proactive investment in production facilities and effective asset management.
For the controlling department, the single point of truth provides greater transparency throughout the entire budgeting process, fostering collaboration and bolstering confidence in financial planning decisions based on reliable data.
By leveraging the Board demand planning solution, BASF Care Chemicals not only optimizes volume planning but also cultivates a culture of efficiency, agility, and informed decision-making. In a competitive industry and an ever-evolving global landscape, this propels the organization toward sustainable growth and profitability.